Modular Floor Structure / Base Platform Installed
/Portion of floor structure showing modules bolted together with control columns and rudder pedals installed to structure
Although it has taken longer than anticipated, the second platform to replace the platform made from wood and MDF fibreboard has been completed.
The new design is constructed from aluminium flat tubing, is modular, and incorporates the mechanical hardware needed for operation of the OEM 737 control columns.
The structure comprises two main sections - the modular floor structure, and floor (called the base platform).
Centre platform with ABS plastic floor structure attached. Note the shiny appearance. This was later removed by painting
The modular design of the platform, which in addition to allowing easy disassembly and transport (if required), also allows the platform to be increased in size by adding further modules. For instance, if I decide to add an instructor station in the future it will be straightforward to manufacture another module and bolt it to the existing framework. The hollow underneath section also provides an ideal area for the hidden storage of wires, power boards, and other pieces of necessary equipment such as external speakers and sound systems.
Two aft modules with flooring fitted, rudder pedals in background on forward command module
Access to the underside of the base platform (floor) is via several well-positioned hatches. Removal of a hatch (4 screws) enables access to whatever is beneath the floor.The platform comprises ten modules which are bolted together at strategic locations to ensure the structure is rigid, strong and sturdy. Each module has several cross stays that have been welded in place ensuring adequate support for the weight which will be placed on the platform (Weber seats, MIP, throttle unit and people).
The first three modules, which I call the command module, have been constructed as one unit and house the rudder pedals, control columns and incorporate the duel linkage rods and other mechanical hardware for control column and rudder pedal operation. Although this unit can be separated into the three modules (by removing the attachment bolts, springs and linkage rods),
Half circle flange and seal around control column and drill holes through floor that match corresponding hole in aluminium framework. Bolts have been used to secure Weber seats. In the second picture of this series, you can see the claw feet secured by four bolts through the flooring to the support beneath
it’s best to leave them attached, as removing the steering mechanism and associated equipment is a complicated and timely operation.
Behind the forward command module are three secondary modules to allow attachment of the two Weber seats and throttle quadrant. The MIP is attached to two smaller and narrower modules bolted at the front of the command module; whilst at each side two longer and narrow modules provide side support.
Platform Height and Dimensions
The height of the platform measures 16 cm (6.3 inches) and the total weight, including the two rudder pedals, internal mechanisms and control columns is approximately 160 kilograms (353 pounds). At this weight, it certainly will not be sliding anywhere.
The platform is not a full size platform as space availability at the current time is limited, however, if and when I wish to move into a full size platform, it will be easy to incorporate and bolt additional correctly sized modules to the existing structure.
Installing Weber Seats
The Weber seats need additional support as seat movement can generate stress at the connection point of the claw feet and floor. To ensure the seats fitted securely and any stress of seat movement was absorbed by the platform and not just the floor structure, the claw feet bolt directly through the floor to the aluminium tubing structure. Therefore, the platform absorbs the stress when the seats are moved rather than the flooring.
Platform Floor - ABS Plastic
In the real aircraft the floor is made from pressed aluminum which is studded (rivets) in strategic locations to ensure it is solidly fixed. Various hatches (hinged and otherwise) are present in certain areas to facilitate access to areas beneath the sheeting.
Builders use many different products for the floor, ranging from MDF fibreboard, ply and aluminium to tin or plastic. I was intending to use thin aluminium sheeting as a platform floor, however, when I discovered the price I decided to use something less conventional.
A supply of heavy duty ABS plastic was readily available; the advantage of this material being it doesn’t require painting as it’s already coloured Boeing grey, is easy to cut and work with, is of a thickness and weight that can withstand the intended weight and finally, doesn’t flex. Rather than use one large sheet of board for the platform cover, which would be unmanageable, the sheet has been cut to fit each corresponding module. The sheets are attached to the aluminium tubing of the module by normal stainless screws. If the material doesn’t hold up to my expectations, I’ll replace it with aluminium or quality ply board.
Although the ABS plastic is coloured grey, I found it to be too shinny in appearance. Preparing the ABS plastic for painting was straightforward and entailed thoroughly cleaning the plastic with detergent to remove any residue oil. Then the plastic was lightly scoured using a low grade sandpaper. This creates a suitable texture for the paint to adhere. The ABS sheeting was then painted with one coast of epoxy plastic primer and two coats of matt Boeing grey.
The ABS plastic and paint has held up to use very well. Even after scuffing, and moving the throttle quadrant onto and off the floor several times the paint and plastic has not been damaged.
One downside of using ABS plastic can be electrostatic discharge. If you wear socks on the platform and rub your feet on the ABS plastic a charge can build-up. I have yet to discover a way to stop this from occurring (other than wearing shoes).
Perhaps I will upgrade the ABS floor at some stage to a full aluminium floor, but at the moment I am more than content with the use of ABS plastic.
Tyre inner tube cut and stretched to fit beneath control column flange. The overlapping area of rubber tube sits over the bulbous part of the control column lever with the floor
Installing the Control Columns, Rudder Pedals and Column Flange
The floor has been cut and the hole shaped to accommodate the control columns and rudder pedals. The various linkage rods and internal mechanisms have either been either bolted or welded directly to the lower platform superstructure.
The half circle flange (or whatever Boeing call it) that surrounds each control column on the floor was constructed from light metal. To replicate the rubber-like seal that is often observed above at the lower end of each control column, a piece of recycled inner tyre tube was used. The rubber was cut and easily stretched to fit beneath the half circle flange.
The Main Instrument Panel (MIP) is secured to the platform by several bolts strategically placed on the MIP.
Computer and Sound System Installation
The two computers that are needed to operate the simulator will be positioned at the front of the platform where access is relatively easy to both power supplies and the MIP. The sound system, which comprises three speakers and a sub-woofer speaker, will be placed directly beneath the floor structure. In the first picture, you can just see the sub-woofer speaker towards the end of the platform.
New Platform Verses Former Platform
The structure of the first platform was from wood, and access to the underside of the platform from the side was next to impossible. The floor was made from two large sheets MDF fibreboard and although sealed and painted, still appeared to release gases (MDF fibreboard releases gas and requires sealing for indoor use). The structure and flooring was very solid, but access to anything beneath the floor (maintenance) was difficult.
To view additional pictures navigate to the image gallery.
BELOW: Diagram layout of modular design.
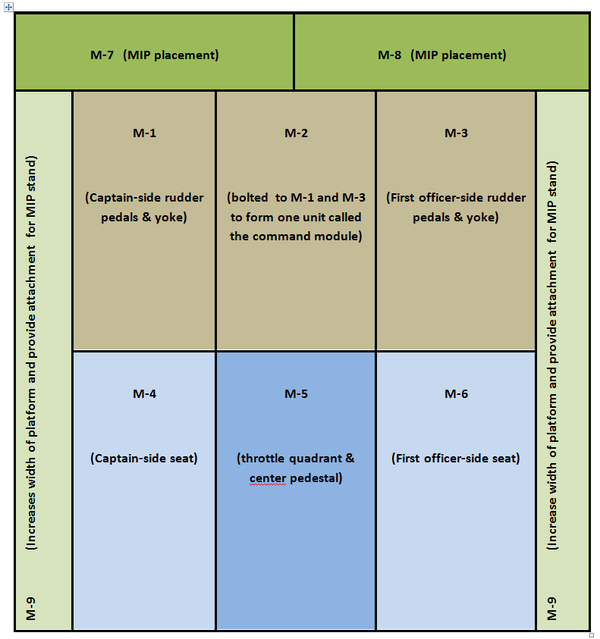
Update
on 2016-07-19 23:25 by FLAPS 2 APPROACH
Several individuals have requested the dimensions of the platform, which is smaller than a standard platform. The benefit on being modular is that you can easily add sections to the platform to increase its size.
Platform Size
Overall Length: 183 cm
Overall Width: 183 cm
Height: 16 cm
Module M7: Overall Length: 183 cm (each piece left and right is 83.5 cm in length)
Module M7: Width 15.5 cm
Module M9: Length 167 cm
Module M9: Width 15.5 cm
Module M1, M2 & M3: Length 85 cm
Module M1, M2 & M3: Width 53 cm
Module M4, M5 & M6: Length 81 cm
Module M4, M5 & M6: Width 53 cm
If you are attempting to accommodate a OEM 737 column linking mechanism, the height of the platform will need to be considerably higher (in the order of 10-12 inches height) to house the lower cog mechanism of the columns.